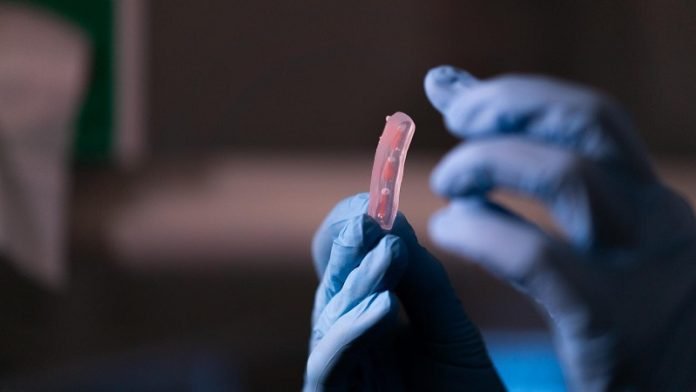
Researchers at EPFL (École Polytechnique Fédérale de Lausanne) have developed a groundbreaking ink that’s set to transform the way soft robots and wearable devices are made.
This new elastomer-based ink allows for 3D printing of objects that are flexible yet durable, without the need for heavy mechanical joints.
In the world of soft robotics and wearable technology, weight is a major concern.
Heavier materials not only use more energy but can also be uncomfortable when worn.
Elastomers, synthetic polymers known for their stretchiness, are ideal for these applications but shaping them into complex structures that vary in stiffness has been a challenge until now.
The team, led by Esther Amstad, head of the Soft Materials Laboratory at EPFL, created an innovative type of ink called double network granular elastomers (DNGEs).
This ink can be printed into structures that change from rigid to rubbery, offering unprecedented control over an object’s mechanical properties.
Eva Baur, a Ph.D. student in Amstad’s lab, demonstrated this technology by 3D printing a prototype “finger” that featured hard “bones” encased in soft “flesh”.
The finger was designed to bend and stretch in specific ways, showcasing the potential of DNGEs to create devices that are both flexible and capable of handling objects.
DNGEs work by combining two different elastomeric networks in a novel way. First, elastomer microparticles are created and then swollen with a special solution.
These swollen particles are then used as the basis for the 3D printable ink. When this ink is used to print a structure, the particles are locked into place by a second polymerization process that forms a rigid framework.
This dual-network setup allows the properties of the elastomer—like stiffness and toughness—to be adjusted independently, resulting in a material that is both tough and flexible. Unlike other materials like hydrogels, elastomers don’t contain water, making them more stable and durable over time.
The technology is compatible with standard commercial 3D printers, making it accessible to a wide range of users. “The beauty of our approach is that anyone with a standard bioprinter can use it,” said Amstad.
The potential applications for DNGEs are vast. They could be used in motion-guided rehabilitation devices that support movement in specific ways, or in prosthetics that offer more natural movement.
They could also be used in surgical aids, remote-operated robots for tasks like crop harvesting or underwater exploration, and more.
As the Soft Materials Lab continues to refine this technology, they plan to integrate active elements like responsive materials and electrical connections into the DNGE structures, broadening the possibilities for future innovations.