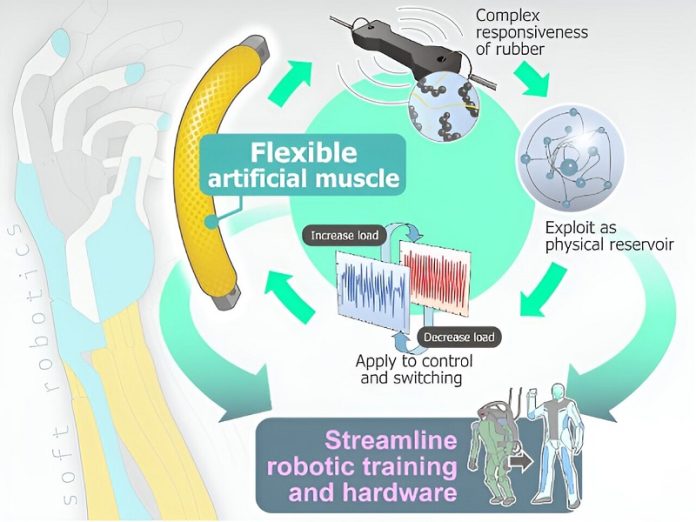
Researchers from Kyoto University, in collaboration with the University of Tokyo and Bridgestone Corporation, have developed a groundbreaking method to control soft robotic actuators, known as pneumatic artificial muscles.
This advancement could revolutionize how robots assist in disaster recovery and interact with humans.
Pneumatic artificial muscles are flexible components that mimic the movement of human muscles using air pressure.
They are ideal for creating robots that need to navigate through and operate in disaster-stricken areas where rigid robots may be too clumsy or dangerous around human survivors.
Traditionally, controlling these soft materials to perform complex tasks has been challenging. Robots typically require external devices called oscillators to create movement patterns such as walking or bending.
However, attaching these devices can make the robots less flexible—which defeats the purpose of using soft materials.
The new method developed by the team removes the need for these external oscillators. Instead, the ability to generate movement patterns is built directly into the muscles of the robot.
“We’ve demonstrated the actuator’s capability to autonomously generate diverse dynamics, including rhythmic patterns and chaos,” said Nozomi Akashi of Kyoto University’s Graduate School of Informatics.
This means the robots can perform a variety of actions on their own, adjusting to different situations without needing preset instructions for every task.
Kohei Nakajima of the University of Tokyo added, “The pattern-changing bifurcation structures can be embedded into the robotic actuator itself.”
This technical achievement allows the artificial muscles to switch between different types of movements depending on the task at hand, much like how human muscles work.
These advancements suggest that robots could soon perform tasks outside of their initial programming, making them much more adaptable and suitable for complex environments such as disaster zones.
Robots with these capabilities could navigate debris, assist in search and rescue operations, or provide emergency support without requiring rigid and heavy components.
“This could streamline the hardware and software development process, making it more efficient and effective,” concludes Akashi.
By integrating the control mechanisms directly into the soft materials, the researchers have simplified the design and functionality of soft robots, potentially leading to faster production and deployment in critical situations.
This breakthrough not only promises to improve the practical application of soft robotics but also opens up new possibilities for machines that can work more harmoniously alongside humans in sensitive and unpredictable environments.