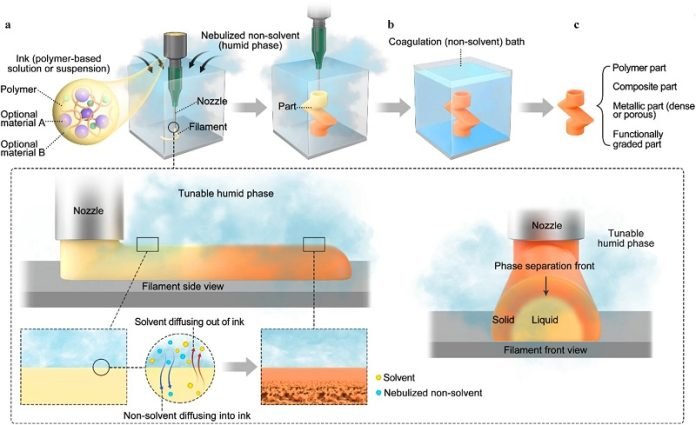
Scientists at the University of Florida have figured out a clever new way to 3D print stuff that could make it a lot cheaper and better for the planet.
This new technique is called vapor-induced phase-separation 3D printing, or VIPS-3DP for short.
It’s a game-changer for making things from single materials to stuff that needs more than one type of material.
Yong Huang, a professor of mechanical and aerospace engineering at the university, and his team are behind this discovery.
They’ve found a way to make 3D printing not just more affordable but also more environmentally friendly. This big news is shared in the journal Nature Communications.
Here’s how it works: Instead of regular ink, they use a special kind of liquid that can dissolve stuff like metal or ceramic particles.
While printing, a certain vapor is introduced which makes the liquid turn solid, creating the object you want. This special moment when the liquid becomes solid is what makes VIPS-3DP stand out.
One cool thing about this method is it lets you make objects that have different materials in different parts. Plus, you can control how spongy or holey these parts are.
This is super useful for making things like medical implants that need to fit nicely with human tissue, or lightweight parts for airplanes.
Marc Sole-Gras, who first authored the study and was a grad student in Huang’s lab, points out how great this is for making metal products with varying levels of sponginess.
An example he gives is making bone implants that can merge well with human cells because they can be made just the right amount of porous.
What makes this new 3D printing method even better is that it’s kinder to the environment and your wallet. It uses less energy and materials that are not harmful to the planet. So, this isn’t just about making 3D printing better; it’s about doing it in a way that’s good for our future.