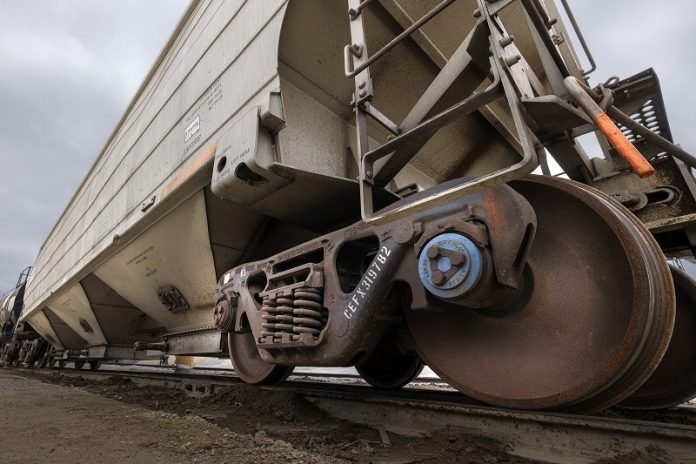
At the University of Nebraska, a team of engineers has made significant advancements in railcar safety and durability by using innovative 3D printing techniques to produce roller bearings.
These components, crucial for the smooth and safe operation of railcars, were traditionally made through conventional manufacturing processes.
However, the Nebraska Engineering team’s use of metal powders and additive manufacturing processes has proven to be just as effective.
Led by Joseph Turner, the Robert W. Brightfelt Professor of Mechanical Engineering, and his team, including recent doctoral graduate Luz Sotelo and other faculty and students, embarked on a project to test whether 3D-printed roller bearings could stand up to the rigorous demands of railway operation.
Their findings were recently published in a paper titled “Fatigue Performance of Bearing Rollers Manufactured by Laser Powder Bed Fusion” in the journal Bearing and Transmission Steels Technology.
The team utilized the state-of-the-art Nebraska Engineering Additive Technology Labs to create these rollers from a high-carbon steel known as 8620HC.
The results were unexpectedly positive, with the 3D-printed rollers performing on par with their traditionally manufactured counterparts.
This achievement has set a promising foundation for further exploration of 3D printing in transportation and other industries.
Traditionally, railcar bearings are crafted by cutting and grinding thick steel wire to form more than 40 rollers per bearing, with around 350 rollers needed per railcar.
The conventional method, although effective, is limited in its flexibility and responsiveness to urgent demands.
The introduction of 3D printing into this process, though currently more expensive, offers several advantages.
One of the potential benefits highlighted by the research is the ability to produce parts on demand, particularly valuable in remote or critical situations where waiting for parts could impede operations, such as in mining activities in remote locations.
The team’s success in proving the viability of 3D-printed bearings under standard fatigue tests—which simulate the loads a railcar might experience over 250,000 miles—marks an important step in the evolution of railcar manufacturing.
Despite initial concerns about the internal structure and durability of printed metals, the rollers held up impressively under the testing conditions.
Looking ahead, the researchers are exploring ways to make 3D printing more cost-effective for mass production.
One idea involves using premium steel powders to create a durable coating on less expensive metal components, potentially reducing overall manufacturing costs while enhancing the product’s performance.
This breakthrough not only showcases the potential of 3D printing in enhancing rail safety and efficiency but also opens up new possibilities for its application across various industries.
As the technology continues to evolve and become more affordable, the Nebraska team’s work could lead to widespread changes in how components are manufactured in many sectors.