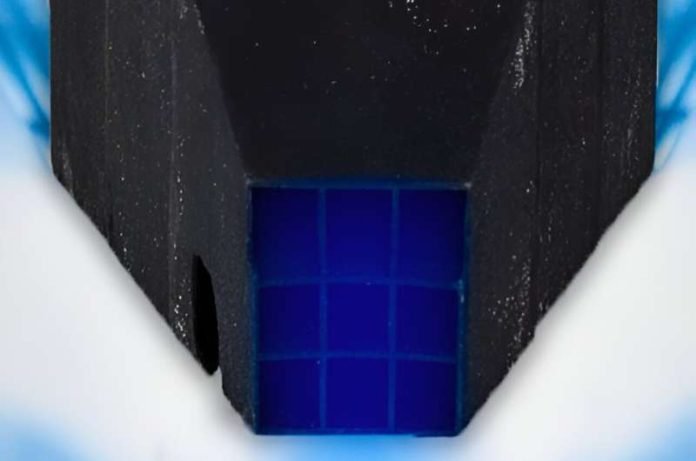
In the world of science, especially at the Department of Energy’s Oak Ridge National Laboratory, a new story of innovation and adaptation has emerged.
Scientists there have taken the age-old strategy of “divide and conquer” and given it a modern twist.
While working on a project to 3D print a tool called a collimator, they ran into a snag. Instead of producing it as one whole piece, they found a clever workaround: they created it from multiple parts, leading to a creation they’ve nicknamed the “Frankenstein design.”
This name not only captures the method of assembling different pieces but also the visible “scars” where these pieces join, much like the fictional character Frankenstein’s monster.
A collimator, in simple terms, is a device used in neutron scattering experiments. Neutron scattering is a technique similar to using X-rays for looking at objects’ internal structures, but it uses neutrons to explore materials at the atomic level.
Collimators work by directing these neutrons in a specific path, much like a funnel, ensuring that only the neutrons interacting with the material being studied reach the detector.
This is crucial for getting clear data, as it helps filter out background noise from neutrons scattering off other objects in the vicinity.
The need for this innovation arose from the challenges of studying smaller samples in complex environments, which led to an increase in unwanted background signals. The traditional approach to building collimators couldn’t filter out this noise effectively.
To address this, the team, including lead author Fahima Islam and her colleagues at the Spallation Neutron Source (SNS), ventured into the realm of 3D printing, specifically using a method known as binder jetting.
This technique builds objects layer by layer from a digital design, allowing for the creation of complex shapes and structures.
Initially, the team attempted to create a large, one-piece collimator to accommodate more neutrons and reduce background noise.
This approach, however, led to precision issues due to the complexities of scaling up the 3D printing process. The larger the piece, the more prone it was to imperfections, such as cracking, due to uneven cooling and curing.
The solution? Break the design into smaller, manageable parts that could be individually printed and then assembled into the final product.
This method not only reduced the risk of imperfections but also allowed for more intricate designs, such as alternating blade configurations that improved the device’s efficiency in guiding neutrons.
This Frankenstein design approach was put to the test with a diamond anvil cell, a high-pressure chamber used to squeeze materials for study.
These cells are notoriously difficult to work with due to the strong scattering of neutrons they produce, which can obscure the data scientists are after. The redesigned collimator needed to be precise, as even slight misalignments could significantly impact its performance.
The final product was a success, demonstrating improved performance in filtering out unwanted neutron scatter and enhancing the clarity of the data collected.
This breakthrough not only showcases the potential of 3D printing in creating custom scientific tools but also marks a significant step forward in neutron scattering research.
By combining traditional scientific principles with modern manufacturing techniques, the Oak Ridge team has opened up new possibilities for neutron science.
The Frankenstein collimator, with its patchwork of precisely crafted parts, stands as a testament to human ingenuity and the relentless pursuit of scientific advancement.
The research findings can be found in Nuclear Instruments and Methods in Physics Research Section A: Accelerators, Spectrometers, Detectors and Associated Equipment.
Copyright © 2024 Knowridge Science Report. All rights reserved.