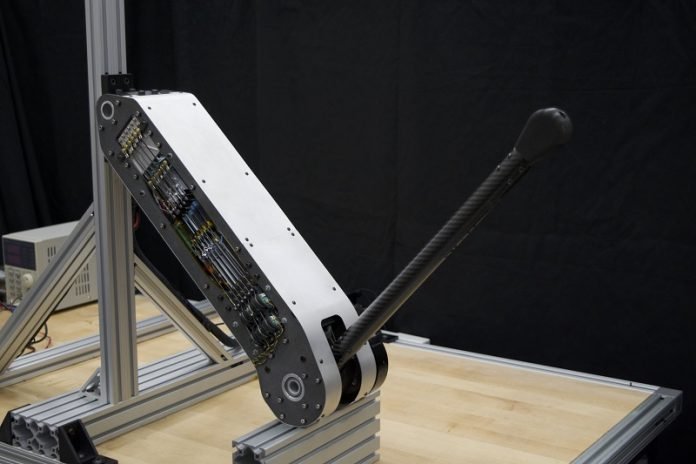
In the quest to make robots and machines do more without gobbling up too much power, researchers at Stanford University have come up with a groundbreaking solution.
They’ve developed a new device that could make robots not just more energy-efficient but also capable of handling more complex tasks with ease.
This invention is especially exciting for everything from robots exploring hazardous environments to powered prosthetics that help people move.
Traditionally, electric motors are the heart of many machines, from household appliances to industrial equipment.
However, they’re not the best at doing tasks that need a lot of starting and stopping or quick, intricate movements. That’s because they tend to waste a lot of energy, which isn’t ideal for tasks requiring finesse or for devices that we hope to run on batteries for a long time.
Enter the brilliant minds at Stanford, who have created a new kind of actuator. An actuator is a component in machines that helps move or control a mechanism or system.
This new actuator, unveiled in the prestigious journal Science Robotics, is not your average motor.
It cleverly uses springs and special clutches to do its job, making it way more efficient at those tricky, dynamic tasks.
Here’s the cool part: springs are great at storing energy when they’re stretched or compressed, and they don’t need electricity to do it.
The Stanford team’s actuator uses this to its advantage. For instance, when the actuator needs to lower a heavy load, it lets the springs stretch and take on some of the weight, which means the motor doesn’t have to work as hard.
Then, by locking the springs in place, it can store that energy for later use, like giving the motor a boost when it needs to lift something.
The secret sauce to this setup is what the researchers call electroadhesive clutches. These are like sophisticated switches that can quickly lock or release the springs as needed.
They work through a kind of electric attraction—when turned on, they stick together firmly, holding the spring in place. When turned off, they let go, all without the need for continuous power.
This design is not only clever but also incredibly efficient. The team’s tests showed that their spring-assisted actuator could use at least 50% less power than traditional motors, and sometimes the savings were as much as 97%!
This means robots could potentially run longer on a single charge, do more, and even venture into places where humans can’t safely go, all while using less energy.
But the researchers aren’t stopping here. They’re working on making their system even smarter, using artificial intelligence to quickly figure out the best way to tackle new tasks by learning from past actions. This could lead to robots that are not just more efficient but also more adaptable.
The team is excited about the potential of their invention.
They’re looking at starting a company to bring their energy-saving actuator to the wider world, promising a future where robots and assistive devices are not only more capable but also much kinder to our planet’s resources.