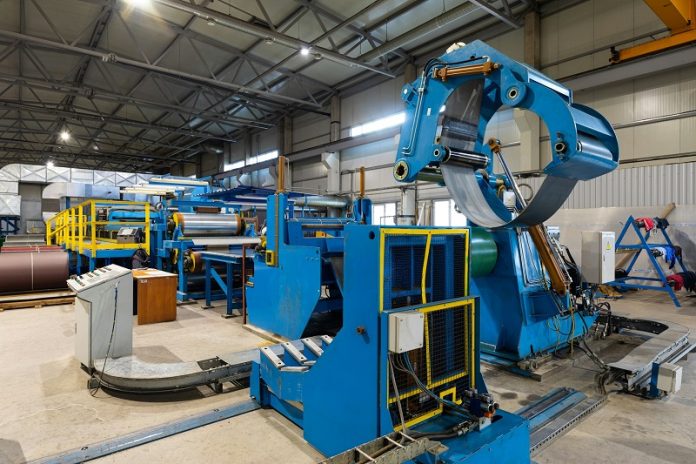
In the world of aerospace manufacturing, cutting through tough materials like titanium alloys, composites, and intricate components is a big challenge.
These materials are essential for building parts that can withstand extreme conditions, but they’re notoriously hard to work with.
The process can be slow, wear out tools quickly, and often results in less-than-perfect surface quality.
Recognizing the need for a better approach, researchers are turning to a groundbreaking method that combines traditional cutting with powerful, nontraditional energies like lasers and vibrations.
A team led by Professor Wenfeng Ding at Nanjing University of Aeronautics and Astronautics has been exploring this innovative technique, known as nontraditional energy-assisted mechanical machining.
Their work, featured in the International Journal of Extreme Manufacturing, introduces a blend of methods that can make tough materials much easier to cut, promising a significant leap forward for aerospace engineering.
This approach works by adding extra energies to the cutting process, which makes the material easier to shape and cut.
For instance, by using vibrations, lasers, or electric currents, the material being cut becomes softer or more pliable at the point of contact with the cutting tool.
This not only makes the cutting process smoother but also helps preserve the tools and improve the final surface quality of the part being made.
For the aerospace industry, where materials need to perform under the most demanding conditions, this method could be a game-changer.
It means parts can be made more efficiently, with less waste and lower costs, while maintaining the high quality needed for aerospace components. This could lead to better aircraft and spacecraft, and potentially, more advancements in how we explore and utilize space.
However, there are hurdles to overcome. Not all materials are suitable for every type of energy-assisted machining. For example, certain ceramics or glasses might not respond well to laser-assisted machining due to their properties.
Moreover, cutting complex shapes still presents a challenge, as it requires precise coordination between the laser and the cutting tool.
To address these issues, the researchers are focusing on designing the process from the ground up to ensure the best match between the cutting method and the material. They’re also working on developing smart equipment that can adapt to the complexities of these cutting tasks.
Despite the progress made, there’s still a long journey ahead from the laboratory to the manufacturing floor. Future research will need to dive deeper into the fundamentals of these processes, seek technical breakthroughs, and create the next generation of machining equipment.
This method represents a fusion of disciplines, from mechanics and physics to chemistry and materials science.
As such, wide-ranging collaboration across these fields will be crucial to bringing these advanced manufacturing techniques into widespread use in the aerospace industry.
In essence, this research is not just about making tough materials easier to cut; it’s about pushing the boundaries of what’s possible in aerospace manufacturing, opening up new possibilities for innovation and efficiency in an industry that’s always looking to reach new heights.