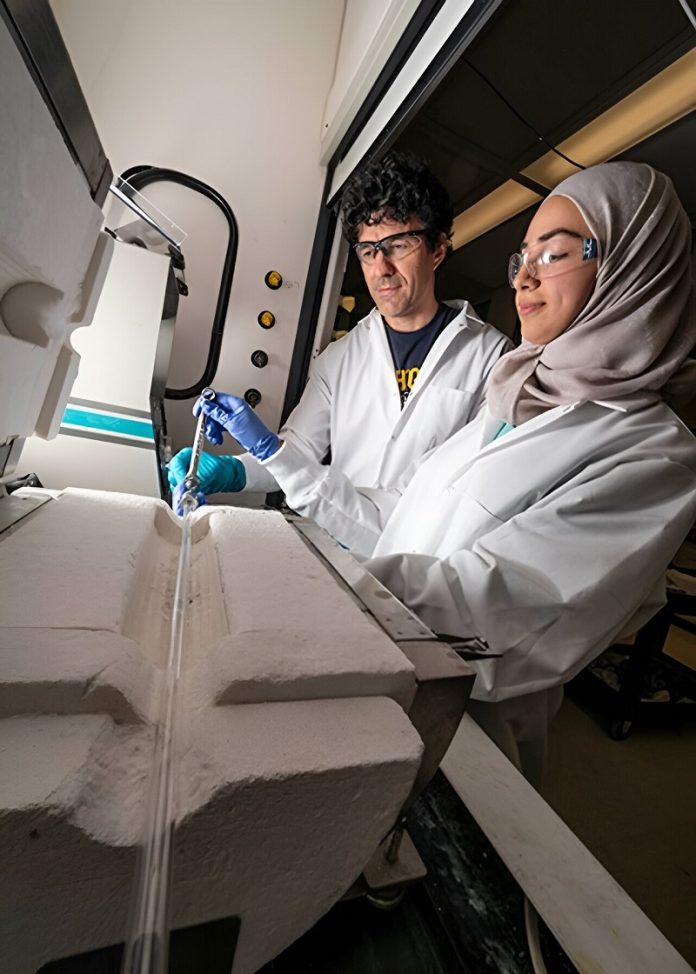
In the world of manufacturing, finding cheaper and more efficient ways to produce essential materials is a constant goal.
Now, engineers from the University of Michigan have made a big leap in how we might make plastics, adhesives, and even rubber gloves in the future.
They’ve designed a new type of chemical reactor that could significantly lower the cost of making propylene, a crucial ingredient in a wide range of products, by using natural gas instead of oil.
Today, propylene is mostly obtained as a byproduct when crude oil is refined into gasoline. It’s a key component not just in plastics and household cleaners, but also in making the nitrile rubber used in car parts and the blue protective gloves you might see doctors wearing.
However, as the world moves away from oil and gasoline in favor of cleaner energy sources like natural gas, wind, and solar power, there’s a concern that we won’t have enough propylene to meet demand.
Natural gas, especially the type extracted from shale, is a promising alternative source because it contains propane, which is very similar to propylene.
But until now, turning propane into propylene wasn’t efficient or cost-effective due to technical challenges.
High temperatures were needed for the conversion, which not only produced unwanted byproducts but also solid carbon deposits that clogged up the catalysts used in the reaction.
Cleaning these out regularly made the process too inefficient to be worth it.
The University of Michigan team’s breakthrough comes with a reactor that cleverly separates propane into propylene and hydrogen gas.
This not only increases the amount of propylene produced but also solves the problem of the unwanted byproducts and carbon build-up.
The reactor uses a special design with nested, hollow-fiber membranes that allow the hydrogen gas to escape and be burned separately, providing the necessary heat for the reaction without the downsides of the old methods.
This innovative setup means that plants could produce propylene directly from natural gas without the need for additional heating equipment.
The researchers estimate that a plant producing 500,000 metric tons of propylene yearly could save as much as $23.5 million by switching to this new method.
Plus, the hydrogen that’s produced and burned off in the process is a cleaner fuel than other options, adding another environmental benefit.
In summary, this new reactor technology not only makes it cheaper and more efficient to produce an important chemical used in a vast array of everyday products but also offers a more environmentally friendly alternative to current methods.
As we continue to look for sustainable solutions in all areas of production, innovations like this are crucial steps toward a cleaner, more cost-effective future.