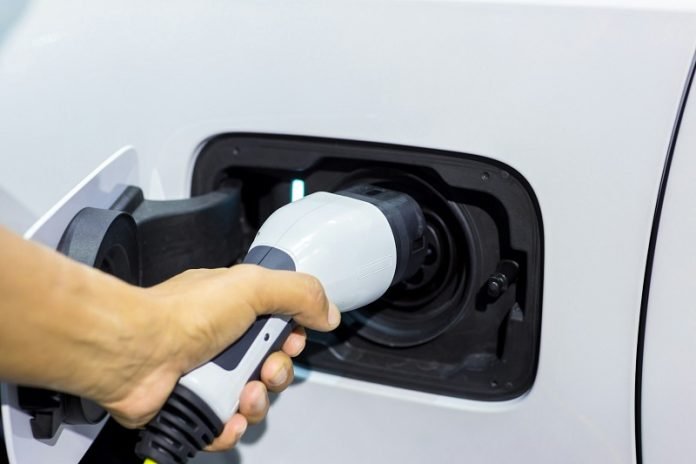
The main cost of an electric vehicle (EV) is its battery.
The high cost of energy-dense batteries has meant EVs have long been more expensive than their fossil fuel equivalents.
But this could change faster than we thought.
The world’s largest maker of batteries for electric cars, China’s CATL, claims it will slash the cost of its batteries by up to 50% this year, as a price war kicks off with the second largest maker in China, BYD subsidiary FinDreams.
What’s behind this? After the electric vehicle industry experienced a huge surge in 2022, it has hit headwinds. It ramped up faster than demand, triggering efforts to cut costs.
But the promised price cuts are also a sign of progress. Researchers have made great strides in finding new battery chemistries.
CATL and BYD now make EV batteries without any cobalt, an expensive, scarce metal linked to child labor and dangerous mining practices in the Democratic Republic of the Congo.
Economies of scale and new supplies of lithium make it possible to sell batteries more cheaply. And the world’s largest carmaker, Toyota, is pinning its hopes on solid-state batteries in the hope these energy-dense, all but fireproof batteries will make possible EVs with a range of more than 1,200km per charge .
How are battery makers cutting costs?
The largest market for electric and plug-in hybrid vehicles is China. But demand for EVs here has eased off, dropping from a 96% surge in demand in 2022 to a 36% rise in 2023.
As a result, battery giant CATL has seen its profits fall for the first time in almost two years.
One of the best ways to create more demand is to make your products cheaper. That’s what’s behind the cost-cutting promises from CATL and BYD.
You might wonder how that’s possible. One of the key challenges in shifting to battery-electric cars is where to get the raw materials. The electric future rests on viable supply chains for critical minerals such as lithium, nickel, copper, cobalt and rare earth elements.
Until recently, the main EV battery chemistry has been built on four of these, lithium, nickel, manganese and cobalt. These are also known as NMC batteries.
If you can avoid or minimize the use of expensive or controversial minerals, you can cut costs. That’s why Chinese companies such as CATL have all but monopolized the market on another chemistry, lithium iron phosphate (LFP) batteries. These batteries are cheaper, as they have no cobalt. They have other benefits too: a longer usable life and less risk of fire than traditional lithium battery chemistries. The downside is they have lower capacity and voltage.
The recent price cuts come from a deliberate decision to use abundant earth materials such as iron and phosphorus wherever possible.
What about lithium? Prices of lithium carbonate, the salt form of the ultra light silvery-white metal, shot up sixfold between 2020 and 2022 in China before falling last year.
Despite this, battery prices have kept falling—just not by as much as they otherwise would have.
The world’s huge demand for lithium has led to strong growth in supply, as miners scramble to find new sources. CATL, for instance, is spending A$2.1 billion on lithium extraction plants in Bolivia.
Growth in lithium supply is projected to outpace demand by 34% both this year and next, which should help stabilize battery prices.
Battery options are multiplying
China’s battery makers have cornered the market in lithium iron phosphate batteries. But they aren’t the only game in town.
Tesla electric cars have long been powered by batteries from Japan’s Panasonic and South Korea LG.
These batteries are built on the older but well established NMC and lithium nickel cobalt aluminate oxide (NCA) chemistries. Even so, the American carmaker is now using CATL’s LFP batteries in its more affordable cars.
The world’s largest carmaker, Toyota, has long been skeptical of lithium-ion batteries and has focused on hybrid and hydrogen fuel cell vehicles instead.
But this is changing. Toyota is now focused heavily on making solid-state batteries a reality. These do away with liquid electrolytes to transport electricity in favor of a solid battery.
In September last year, the company announced a breakthrough which it claims will enable faster recharging times and a range of 1,200km before recharge. If these claims are true, these batteries would effectively double the range of today’s topline EVs.
In response, China’s battery manufacturers and government are working to catch up with Toyota on solid-state batteries.
Which battery chemistry will win out? It’s too early to say for electric vehicles. But as the green transition continues, it’s likely we’ll need not just one but many options.
After all, the energy needs of a prime mover truck will be different to city runabout EVs. And as electric aircraft go from dream to reality, these will need different batteries again. To get battery-electric aircraft off the ground, you need batteries with a huge power density.
The good news? These are engineering challenges which can be overcome. Just last year, CATL announced a pioneering “condensed matter” battery for electric aircraft, with up to three times the energy density of an average electric car battery.
All the while, researchers are pushing the envelope even further. A good electric car might have a battery with an energy density of 150–250 watt-hours per kilogram. But the record in the lab is now over 700 watt-hours/kg.
This is to say nothing of the research going into still other battery chemistries, from sodium-ion to iron-air to liquid metal batteries.
We are, in short, still at the beginning of the battery revolution.
Written by Muhammad Rizwan Azhar, Waqas Uzair and Yasir Arafat, The Conversation.