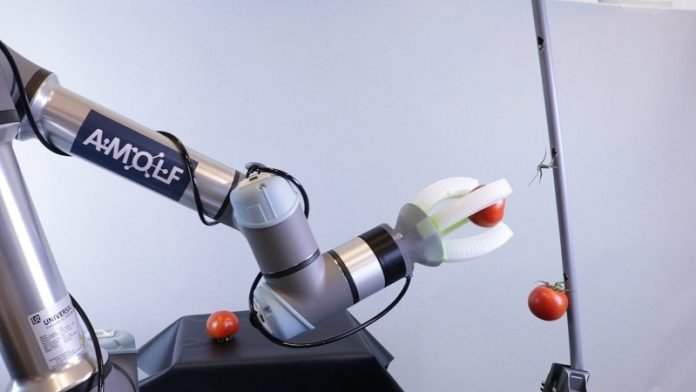
In a world where robots are becoming more and more integrated into our daily lives, a groundbreaking development has emerged from the labs of the AMOLF Soft Robotic Matter Group.
Researchers Shibo Zou and Bas Overvelde, in collaboration with the Eindhoven University of Technology, have unveiled a novel approach that allows soft robot fingers to “feel” their surroundings without needing any internal sensors.
This breakthrough, detailed in Nature Communications, is set to transform the way robots interact with the world around them.
Imagine trying to pick a ripe tomato or avocado without squishing it; it requires a delicate touch, a sense of how hard to squeeze.
This is the challenge that soft robots face, especially in tasks like automated harvesting where the gentleness of the grip is crucial.
Until now, robots needed sensors built into their fingers to tell them about the ripeness of a fruit or the firmness of an object. However, sensors can be hard, bulky, and not always suitable for all applications, such as those involving food or medical procedures.
The new technique developed by Zou, Overvelde, and their team sidesteps these challenges by measuring the interaction of robots with their environment externally. Instead of relying on internal sensors, they use a clever system that measures the air pressure needed to move the robot’s inflatable fingers.
These fingers work like balloons – they inflate to grip objects. When they encounter resistance, like gripping a tomato, it requires more pressure to inflate them, similar to how it’s harder to blow up a balloon while squeezing it. By measuring this pressure, the robot can understand what it’s touching and how firmly it needs to grip.
This method is brilliantly simple yet effective. It allows the robot to determine not just how to handle objects gently but also to make decisions based on what it “feels.” For example, a soft gripper equipped with this technology can pick tomatoes by carefully gripping them with its balloon-like fingers and then plucking them.
The system measures the pressure during this process, enabling the robot to know if it’s holding the tomato correctly. It can even sort tomatoes based on their ripeness, setting aside those that are overripe because they require less pressure to grip.
One of the most exciting applications of this sensor-free technique is in medical procedures. The team has shown that it can be used to control a miniature suction cup for minimally invasive surgeries, such as endoscopies. This suction cup can now “feel” the type of tissue it grips, greatly reducing the risk of tissue damage.
What makes this approach so revolutionary is its versatility. The external pressure measurement system is a plug-and-play solution that can be added to a wide range of existing soft robots without significant modifications. This eliminates the need for custom-built sensors for each new application, whether it be in agriculture, medicine, or beyond.
By removing the reliance on internal sensors, the AMOLF and Eindhoven University of Technology researchers have opened up a new world of possibilities for soft robotics. Their work paves the way for more adaptable, efficient, and sensitive robots capable of performing tasks with a level of delicacy previously unattainable.
As they continue to refine this technology, we can expect to see soft robots taking on an even greater variety of roles in our lives, from the farm to the operating room.