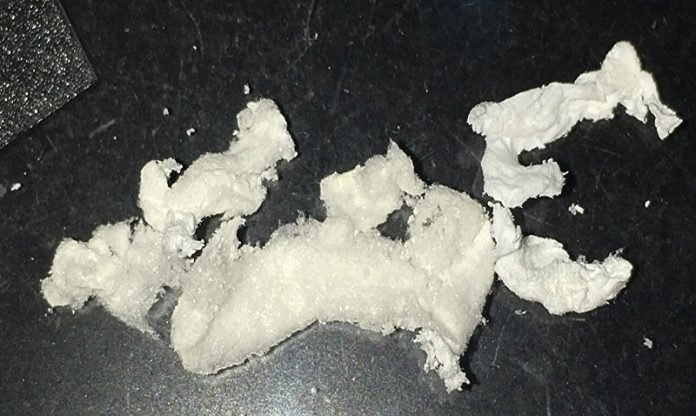
Researchers at Rensselaer Polytechnic Institute have made a groundbreaking discovery: they’ve engineered a type of bacteria that can turn plastic waste into a versatile material similar to spider silk.
This significant study, published in Microbial Cell Factories, is the first of its kind where bacteria have been used to transform polyethylene plastic—common in single-use items—into a valuable protein product.
This new material, which the researchers call “bio-inspired spider silk,” could have many uses, including in textiles, cosmetics, and medicine.
According to Helen Zha, Ph.D., assistant professor of chemical and biological engineering at RPI and one of the project’s leaders, spider silk is an incredible natural material.
It’s almost as strong as steel but much lighter, stretchy, tough, non-toxic, and biodegradable.
Polyethylene plastic is a major environmental concern as it’s found in products like plastic bags and food packaging and takes over a thousand years to decompose naturally. Only a small fraction is recycled. The bacteria used in this study could help recycle more of this waste.
The bacteria, called Pseudomonas aeruginosa, can naturally consume polyethylene. The RPI team modified these bacteria to turn the carbon in polyethylene into a silk protein.
Surprisingly, the bacteria produced the silk protein at rates comparable to other bacteria typically used in bio-manufacturing.
The process behind this is similar to fermentation, which has been used for thousands of years to make foods like cheese, bread, and wine. Mattheos Koffas, Ph.D., another leader of the project, explains that the bacteria essentially ferment the plastic.
However, before this can happen, the plastic needs to be broken down into smaller pieces, just like how we need to chew our food.
The team collaborated with Argonne National Laboratory to break down the plastic by heating it under pressure, creating a soft, waxy substance. This wax was then used as a nutrient source for the bacteria. Typically, fermentation uses sugars, but in this case, the bacteria were fed the plastic-derived wax.
After 72 hours of fermentation, the bacteria were removed, leaving behind the silk protein. This protein, which looked like torn-up cotton balls, could potentially be spun into thread or shaped into various forms.
Zha highlights the eco-friendliness of this process. Unlike traditional plastic production, it’s low-energy and doesn’t require toxic chemicals. The bacteria are effectively doing the work of converting polyethylene into spider silk, a task that would be extremely difficult for even the best human chemists.
Before this bio-upcycled spider silk can be turned into products, the researchers need to find ways to make the silk protein more efficiently. Koffas says that future work will focus on scaling up production by tweaking the bacteria or other parts of the process.
Shekhar Garde, Ph.D., dean of RPI’s School of Engineering, commends the work of Professors Zha and Koffas. Their innovative approach combines biological engineering and materials science to create eco-friendly products, reduce environmental impact, and lessen our dependence on non-renewable resources.
This pioneering study was conducted by Alexander Connor, who earned his doctorate from RPI in 2023, and co-authors Jessica Lamb and Massimiliano Delferro from Argonne National Laboratory.
Their work marks a significant step towards sustainable solutions for plastic pollution and the creation of innovative, eco-friendly materials.