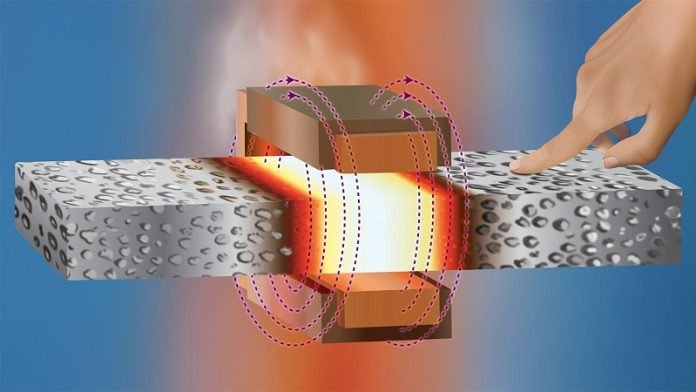
At North Carolina State University, a team of researchers has made an exciting breakthrough in the field of materials engineering.
They have discovered a new way to weld a special kind of metal, known as composite metal foam (CMF), without losing any of its unique properties.
Imagine a sponge made of metal. That’s what CMF is like. It’s a foam that contains tiny, hollow spheres made of tough metals like stainless steel or titanium.
These spheres are set in a base of other metals like steel, titanium, or aluminum.
This combination makes CMF very light but also incredibly strong. It’s like having the strength of a heavy metal, but with much less weight.
Why is CMF Important?
CMF has a lot of potential uses because of its special features.
Its air-filled structure makes it a great insulator against high temperatures, making it useful for things like aircraft wings, protective armor for vehicles, and even body armor.
Plus, it’s great for handling and transporting sensitive materials like nuclear substances, hazardous chemicals, and explosives, because it can protect against heat.
There’s been a big problem, though, when it comes to using CMF in practical applications: welding.
In order to build something out of CMF, you need to join multiple pieces together. Traditional welding methods, which melt the metal to fuse it, don’t work well with CMF. They end up filling in the foam’s air pockets and taking away all the good qualities that make CMF useful.
Here’s where the NC State researchers made their breakthrough. They found a way to weld CMF using a technique called induction welding. This method uses an electromagnetic field to heat the metal, created by an induction coil. It’s different from traditional welding because it doesn’t directly melt the metal with heat.
With induction welding, the electromagnetic field heats the metal in CMF just enough to weld it without damaging the air pockets.
Since CMF is only about 30%-35% metal, the electromagnetic field can get deep into the material, allowing for a solid weld. The air pockets, which make up the rest of CMF, act like an insulator. They keep the heat from spreading, which helps preserve the foam’s structure and qualities.
This new way of welding is a game-changer for CMF. It means that all the benefits of CMF can be fully utilized without compromising its strength, lightness, or insulating properties. This could open the door to many new applications and innovations, particularly in areas where weight, strength, and heat resistance are crucial.
The work done by these researchers is not just a technical achievement; it’s a step towards new possibilities in material science and engineering.
It shows how a deeper understanding of materials and innovative thinking can solve practical problems and create new opportunities.
Source: North Carolina State University.