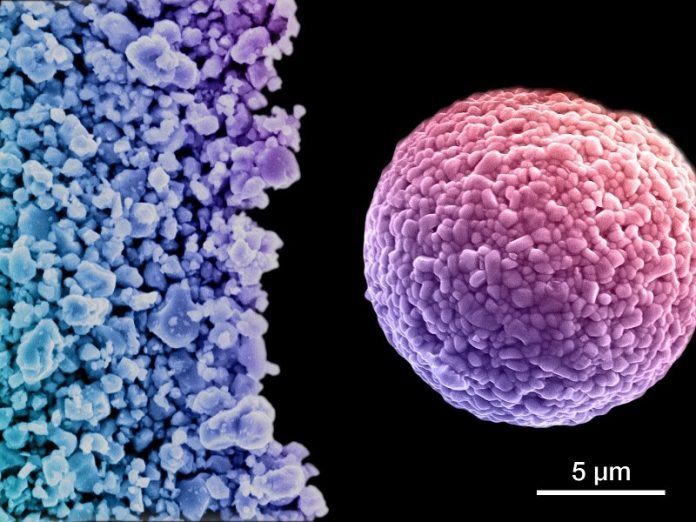
Electric vehicles (EVs) are becoming more popular, but their batteries need to last longer and charge more times to make a difference.
Researchers at the Department of Energy’s Pacific Northwest National Laboratory (PNNL) have made a significant breakthrough that could help.
They’ve found a way to improve the batteries’ energy storage and durability, as their recent paper in Energy Storage Materials describes.
The secret lies in the battery’s cathode, a key component in lithium-ion cells, which are the most common type of EV battery.
The cathode is like the heart of the battery, and most limitations come from regarding how much energy the battery can store and how much it costs.
Nickel-Rich Batteries: The Future of EVs
Researchers focus on cathodes that have more nickel to store more energy. These nickel-rich cathodes can boost the battery’s energy capacity, which means EVs can go further on a single charge.
But there’s a problem: making these high-nickel cathodes often results in a lumpy, rough texture. While this might work for regular cathodes, the lumpy ones with lots of nickel can crack and degrade faster.
The researchers thought that if they could make these cathodes smooth instead of lumpy, they could stop them from cracking.
In labs, scientists can grow these smooth cathodes using special methods, which aren’t practical for large-scale manufacturing. Typically, manufacturers mix metal hydroxide with lithium salt and heat it, which results in the lumpy texture.
A Simple Yet Innovative Solution
PNNL’s team, working with Albemarle Corporation, found a way around this. They added a pre-heating step that changes the metal hydroxide’s structure. When this pre-treated material mixes with lithium salt, it forms smooth, single-crystal cathodes instead of lumpy ones.
Yujing Bi, the study’s first author, explains that this process might seem simple but involves complex atomic-level changes. The best part is that it’s easy for manufacturers to adopt.
The researchers are now scaling up their method to make larger amounts of these cathodes, using lithium salt from Albemarle.
They tested these new cathodes in realistic 2Ah lithium-ion pouch cells, paired with a standard graphite anode. This was to ensure the performance improvements came from the new cathode.
The results were impressive. The prototype battery with these cathodes was stable even after 1,000 charge and discharge cycles. Microscopic examinations showed that the crystals remained defect-free and perfectly aligned.
Stan Whittingham, a Nobel Laureate in chemistry, praised this breakthrough, saying it’s crucial for long-lasting batteries in EVs and for integrating them with renewable energy sources.
This new method for creating single-crystal, nickel-rich cathodes is innovative, cost-effective, and scalable.
It fits right into existing manufacturing processes, making it easier for companies to start producing these improved cathodes. The team plans to start commercial-scale synthesis and testing in early 2024, using conventional manufacturing equipment but with their new technique.
Jie Xiao, the principal investigator of the project and a Battelle Fellow at PNNL, emphasizes that this is just part of their ongoing research in cathode technology.
Along with Albemarle, they’re tackling the challenges of synthesis and scale-up, aiming to reduce manufacturing costs from raw materials.
This development marks a significant step forward in EV battery technology.
It promises longer-lasting batteries and a significant boost to the range and reliability of electric vehicles, bringing us closer to a more sustainable, electric-powered future.