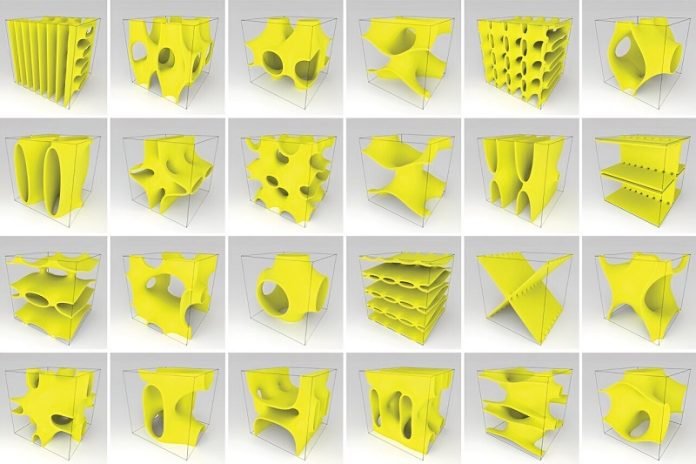
Imagine a world where we have materials so light yet strong that they make airplanes and cars use less fuel.
Or, a material that is so friendly to the human body that it can be used for bone implants.
Well, we are getting closer to that reality thanks to some clever folks at MIT and the Institute of Science and Technology Austria.
These smart people have come up with a way to build what are called “cellular metamaterials”. These are structures made from tiny repeating units or cells.
However, figuring out which cell structure will give you the properties you want is like finding a needle in a haystack.
You see, even if you only look at structures made from small parts like beams or thin plates, there are endless ways you can arrange them. So, engineers can only try out a small fraction of all the possible structures.
But, these researchers have developed a new technique that acts like a specialized computer design system for these cellular metamaterials.
This allows an engineer to quickly model and experiment with designs that might have otherwise taken days to come up with. It’s like having a digital sandbox to play with all kinds of building blocks.
The team found a way to represent all the different shapes engineers usually work with. Because you can build them all the same way, it means you can switch between them more smoothly.
“It’s like having all the pieces of a Lego set at your fingertips, and you can build anything you want,” explains Liane Makatura, a grad student at MIT who co-wrote a paper on the technique.
They discovered that the complex shapes in these structures could be simplified down to lower-dimensional shapes—like how a beam could be seen as just a line or a thin-shell squished down to a flat surface.
They also noticed that many of these structures have symmetries, so you only need to represent a small part, and the rest can be built by repeating that initial piece.
With their new method, a user builds a metamaterial skeleton using building blocks created by points (vertices) and lines (edges).
For example, to make a beam structure, you place a point at each end of the beam and connect them with a line. Then you use a function to specify the thickness of the beam, which can be varied so one part of the beam is thicker than another. The process for surfaces is similar.
The new system also lets users quickly build a very complex type of metamaterial called a triply periodic minimal surface (TPMS). These structures are super powerful, but they are usually hard to make and often fail.
Once a user finishes their design, the system shows the entire procedure they took to get there—all the points, lines, transformations, and thickening operations.
In a user-friendly interface, designers can preview their structure at any point in the process and predict certain properties, like how stiff it is. They can then adjust some parameters and check it again until they get the design they want.
The researchers tested their system and found that it only took seconds to generate each metamaterial structure. They also let automated exploration algorithms loose in their system and one test returned more than 1,000 potential structures in about an hour.
In a user-study with 10 individuals who were new to modeling metamaterials, the users could successfully model all six structures they were given. Most agreed that the new method made the process easier.
In the future, the researchers want to enhance their technique to model a wider variety of shapes and explore the use of automatic generation algorithms.
Their long-term goal is to use this system to specify desired material properties and then use an algorithm to find the best metamaterial structure. So, this tool could be a game-changer in material design!
Follow us on Twitter for more articles about this topic.
Source: MIT.