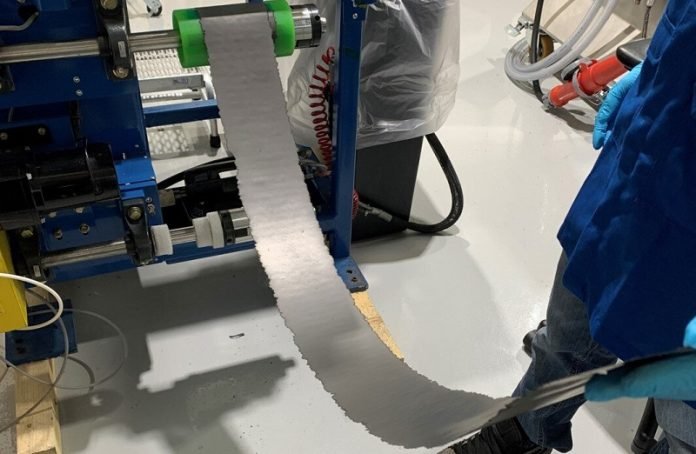
Electric vehicles (EVs) are crucial for achieving a clean energy future, and their performance largely relies on advanced lithium-ion batteries.
However, the traditional wet manufacturing process used to create battery electrodes involves toxic solvents, posing environmental and health risks while driving up costs.
Excitingly, researchers at the Department of Energy’s Oak Ridge National Laboratory (ORNL) have made significant progress in developing a dry battery manufacturing process.
This innovative approach eliminates solvents, offering a more sustainable and affordable method to produce high-energy batteries.
By enhancing EV adoption, this breakthrough can contribute to reducing carbon emissions and helping the United States achieve its climate goals. Let’s explore the details of this game-changing research.
Dry processing is an emerging alternative that offers numerous advantages, including space, time, energy, and waste reduction, as well as lower startup expenses. Despite its potential, researchers have had limited knowledge of how and why it works—until now.
ORNL, in collaboration with industry partner Navitas Systems, investigated the effects of the dry process on battery materials’ structure and electrochemical properties.
Batteries generate energy as lithium ions travel between electrodes known as the cathode and anode.
The team focused on an electrode dry processing strategy, involving mixing dry powders with a binder and compacting the material to enhance particle contact. This technique could be applied to both the anode and cathode using specific materials or mixing methods.
After Navitas created the electrodes, ORNL researchers, led by Jianlin Li and Runming Tao, assessed their electrochemical performance under various conditions and over different timeframes. The findings revealed that batteries manufactured using the dry process exhibited remarkable capacity retention, even after extended use.
Researchers discovered that the dry process batteries possess a highly desirable chemical structure, allowing lithium ions to take a more direct path between the anode and cathode. The thicker electrodes enable higher energy loading while reducing inactive components that contribute to size and weight increase.
The dry process offers a host of benefits for manufacturers and the U.S. supply chain. It is compatible with existing state-of-the-art electrode manufacturing equipment, making it easier to implement. Additionally, its reduced environmental impact allows battery plants to be established in more locations.
Further research aims to stabilize the material that connects the anode components to a thin metal current collector. The team also seeks to reduce the amount of carbon black, a material that maintains battery conductivity but decreases energy density.
Researchers at ORNL and Navitas are continually refining the process to enhance electrochemical performance. They strive to strike a balance between the advantages and drawbacks of thicker electrodes, as they enable higher energy loading but may result in slower power delivery due to increased ion travel distances.
The advent of dry battery manufacturing marks a significant advancement in the field of electric vehicle batteries. By eliminating toxic solvents and offering a more efficient, cost-effective, and sustainable manufacturing approach, this breakthrough paves the way for widespread EV adoption.
With ongoing research and development, scientists are working to optimize the dry process, unlocking the full potential of high-energy, long-lasting batteries. This transformative technology promises to revolutionize the automotive industry and contribute to a greener future.
The research was published in the Chemical Engineering Journal.
Follow us on Twitter for more articles about this topic.