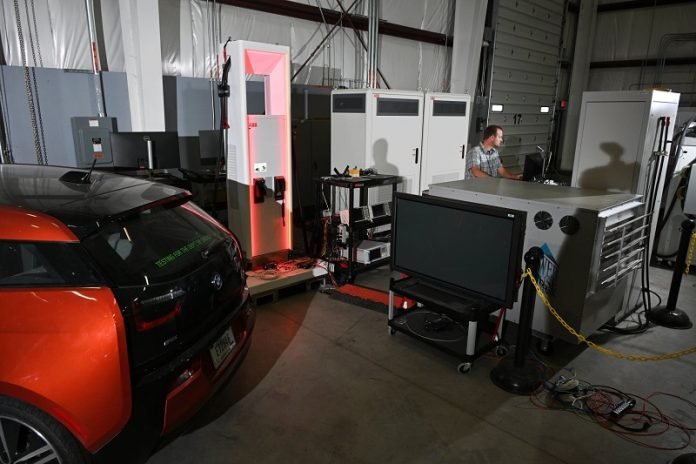
Developing electric vehicle (EV) batteries that can charge as quickly as filling a car with gasoline holds the key to accelerating the adoption of EVs.
Researchers at the Idaho National Laboratory have discovered that high-nickel, layered-oxide cathode materials, particularly NMC811 (80% nickel, 10% manganese, 10% cobalt), offer improved performance, longer lifespan, and faster charging capabilities.
Understanding the properties of these materials is crucial for unlocking their potential in creating high-performance EV batteries.
This breakthrough could address one of the biggest challenges in the EV industry—developing batteries that can recharge in just 10 to 15 minutes.
The need for fast charging
As the world embraces electric vehicles, the demand for faster and more convenient charging solutions is increasing.
While EV sales are on the rise, the ability to charge a battery rapidly remains a significant hurdle.
Extreme fast charging places immense stress on battery components, and optimizing the chemistry, materials, and engineering of electrodes is critical to achieving exceptional performance.
The role of cathodes
In a lithium-ion battery, ions move between the cathode and anode through the electrolyte to provide power.
While researchers are beginning to understand the impact of extreme fast charging on anodes, less is known about its effect on cathodes.
The Idaho National Laboratory (INL) team, led by Tanvir Tanim, has published a study in Advanced Energy Materials, exploring how NMC811 cathodes behave under extreme fast charging conditions and how different materials degrade during the process.
The INL-led team evaluated the aging behavior of NMC811 cathodes under various fast charging rates, including conditions equivalent to over 200,000 miles of driving.
Using advanced electrochemical techniques and scanning electron microscopy, they analyzed failure mechanisms and observed particle architecture changes.
Surprisingly, NMC811 exhibited greater subsurface degradation but demonstrated superior cycle life performance compared to NMC532 (50% nickel, 30% manganese, 20% cobalt), the more common cathode material five years ago.
Despite subsurface degradation, NMC811 showed several advantages. The arrangement of molecules in NMC811 created more accessible pathways for lithium-ion movement, leading to improved cycle life performance.
NMC811 also exhibited higher electrical and ionic conductivity, enabling the battery to hold more charge with repeated use.
Moreover, NMC811 demonstrated slower impedance growth, indicating lower internal resistance, less heating, and higher cell capacity. Its higher specific energy and electrical conductivity, combined with lower cobalt content, also make it a cost-effective option.
The research conducted by the INL team, which is shared with the scientific community, battery developers, and the automotive industry through the U.S. Department of Energy, holds significant relevance for the EV industry. Some automakers have already started using NMC811 cathodes.
The researchers conclude that NMC811 cathodes hold promise for developing EV batteries that can charge in just 10 to 15 minutes.
They offer greater flexibility for optimizing batteries in terms of energy capacity and power delivery.
Future research will focus on understanding the influence of grain orientation and architecture on single-particle performance.
By delving deeper into these factors, scientists aim to further enhance the performance of NMC811 cathodes.
Ultimately, NMC811 has the potential to revolutionize the EV industry by enabling fast charging and improving the overall efficiency and affordability of EV batteries.
Source: KSR.