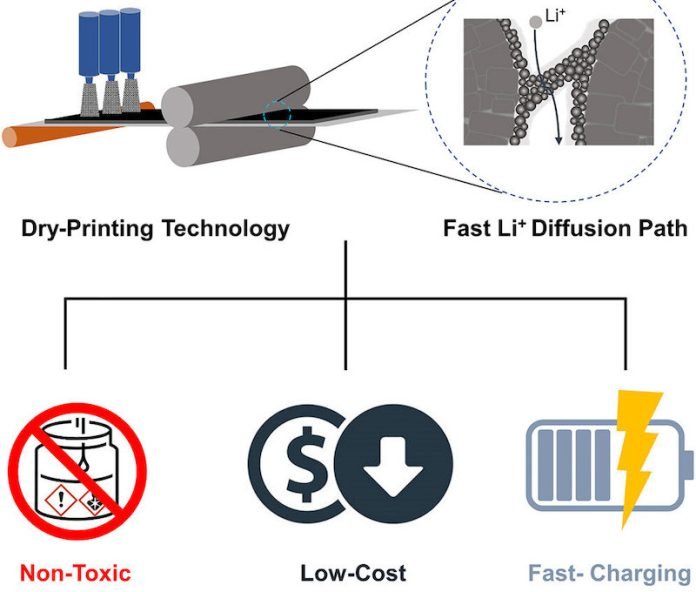
A research group led by Yan Wang at the Worcester Polytechnic Institute (WPI) has come up with a novel, eco-friendly process to produce lithium-ion battery electrodes.
These new electrodes are cheaper and charge faster than their current counterparts, and their introduction could significantly influence battery manufacturing for electric vehicles.
In the scientific journal Joule, the team detailed a solvent-free, dry-print manufacturing method.
This new technique eliminates the need for toxic solvents and lengthy drying times, common hurdles when using traditional methods to manufacture electrodes with slurries.
Wang, who is the WPI William B. Smith Dean’s Professor in the Department of Mechanical and Materials Engineering, believes this innovative process could scale up, leading to a potential 15% reduction in electrode manufacturing costs.
Moreover, these newly produced electrodes could charge much quicker than those generated by traditional methods.
Why it Matters
Wang explained, “Current lithium-ion batteries charge too slowly, and manufacturers typically use flammable, toxic, and expensive solvents that increase the time and cost of production.”
The newly introduced solvent-free process is the answer to these disadvantages. It can produce electrodes that charge up to 78% of capacity in just 20 minutes, and it doesn’t require solvents, slurries, or long production times.
How it Works
Commercial lithium-ion battery electrodes are usually created by combining active materials, conductive additives, polymers, and organic solvents.
This mixture creates a slurry that’s spread onto a metal substrate, dried in an oven, and cut into pieces for battery use. The solvents are then recovered through a distillation process.
On the other hand, the team’s method involves combining electrically charged dry powders. The powder sticks when sprayed onto a metal substrate.
Then, the dry-coated electrodes are heated and compressed using rollers.
This method, which skips the traditional drying and solvent-recovery process, slashes battery manufacturing energy consumption by an estimated 47%, according to the researchers report.
A Commitment to Greener Batteries
Wang has a history of seeking ways to enhance lithium-ion batteries and minimize the waste they generate. He co-founded Ascend Elements, a company focused on developing battery recycling technologies.
With this new breakthrough, the vision of greener, more efficient lithium-ion batteries inches closer to reality.
The study was published in Joule.
Copyright © 2023 Knowridge Science Report. All rights reserved.