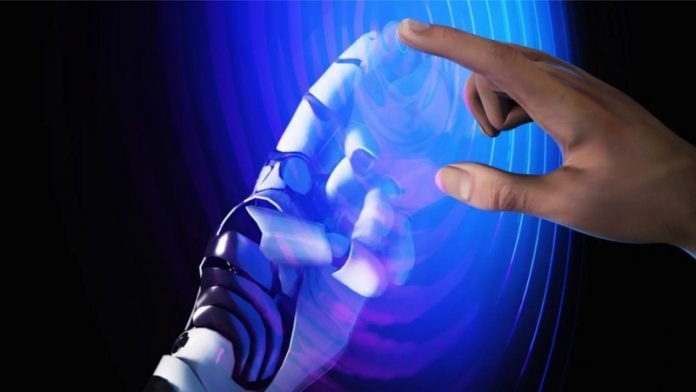
Researchers have discovered a new law of physics that accounts for the friction that occurs when robots grip wet objects.
Although robotic devices are part of processes like assembly lines and medicine, engineers have a hard time accounting for this kind of friction.
“Our work here opens the door to creating more reliable and functional haptic and robotic devices in applications such as telesurgery and manufacturing,” says Lilian Hsiao, an assistant professor of chemical and biomolecular engineering at North Carolina State University and corresponding author of a paper on the work in Nature Materials.
At issue is something called elastohydrodynamic lubrication (EHL) friction, which is the friction that occurs when two solid surfaces come into contact with a thin layer of fluid between them.
This would include the friction that occurs when you rub your fingertips together, with the fluid being the thin layer of naturally occurring oil on your skin.
But it could also apply to a robotic claw lifting an object coated with oil, or to a surgical device working inside the human body.
One reason friction is important is because it helps us hold things without dropping them.
“Understanding friction is intuitive for humans—even when we’re handling soapy dishes,” Hsiao says. “But it is extremely difficult to account for EHL friction when developing materials that controls grasping capabilities in robots.”
To develop materials that help control EHL friction, engineers would need a framework that can be applied uniformly to a wide variety of patterns, materials, and dynamic operating conditions.
And that’s exactly what the researchers have discovered.
“This law can be used to account for EHL friction, and can be applied to many different soft systems—as long as the surfaces of the objects are patterned,” Hsiao says.
In this context, surface patterns could be anything from the slightly raised surfaces on the tips of our fingers to grooves in the surface of a robotic tool.
The new physical principle, which Hsiao developed with graduate student and first author of the paper Yunhu Peng, makes use of four equations to account for all of the physical forces at play in understanding EHL friction.
In the paper, the research team demonstrate the law in three systems: human fingers; a bio-inspired robotic fingertip; and a tool called a tribo-rheometer, which measures frictional forces.
“These results are very useful in robotic hands that have more nuanced controls for reliably handling manufacturing processes,” Hsiao says.
“And it has obvious applications in the realm of telesurgery, in which surgeons remotely control robotic devices to perform surgical procedures. We view this as a fundamental advancement for understanding touch and for controlling touch in synthetic systems.”
Additional coauthors of the paper are from NC State; the University of California, Santa Barbara; and the University of California, Los Angeles.
Support for the work came from the AAAS Marion Milligan Mason Award and the National Science Foundation.