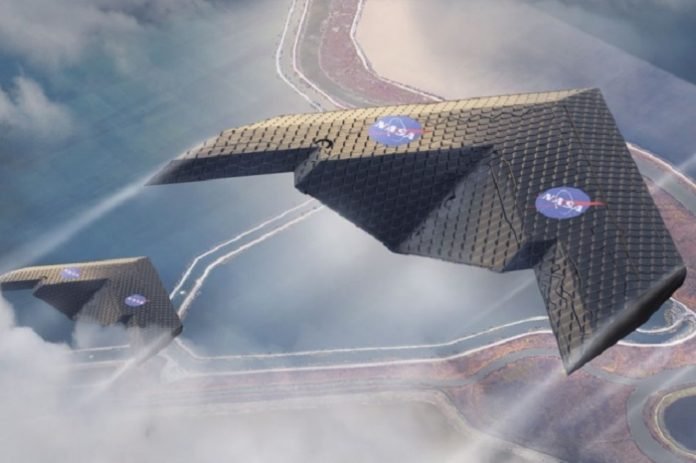
In a new study, a team of engineers from MIT and NASA has developed a radically new kind of airplane wing, which is assembled from hundreds of tiny identical pieces.
The new wing can change shape to control the plane’s flight.
The new finding may provide a big boost in aircraft production, flight, and maintenance efficiency.
In the study, the new wing is about five times as long. It is comparable in size to the wing of a real single-seater plane and could be easy to manufacture.
It was designed to be as large as could be accommodated in NASA’s high-speed wind tunnel at Langley Research Center, and it performed even a bit better than predicted.
The assembly system of the wing could deform the whole wing or parts of it by incorporating a mix of stiff and flexible components in its structure.
The new wing is much lighter and much more energy efficient than wings with conventional designs.
The team explains that for each of the phases of a flight, the wing has a different set of optimal wing parameters to guarantee efficiency.
A swarm of small, simple autonomous assembly robots was used to produce the wing.
Because the overall configuration of the wing or other structure is built up from tiny subunits, it really doesn’t matter what the shape is.
Previous studies have shown that an integrated body and wing structure could be much more efficient for many applications. With this system, the body and wing could be easily built, tested, changed, and retested.
The research shows promise for cutting cost and increasing the performance for large, lightweight, stiff structures.
The team suggests that the new method to wing construction could afford greater flexibility in the design and manufacturing of future aircraft.
The lead author of the study is research engineer Nicholas Cramer at NASA Ames in California.
The study is published in the journal Smart Materials and Structures,
Copyright © 2019 Knowridge Science Report. All rights reserved.